How to Seamlessly Integrate Quality Management into Your Dynamics 365 Workflow
- Krista Galon
- Mar 8
- 4 min read
Updated: Mar 10
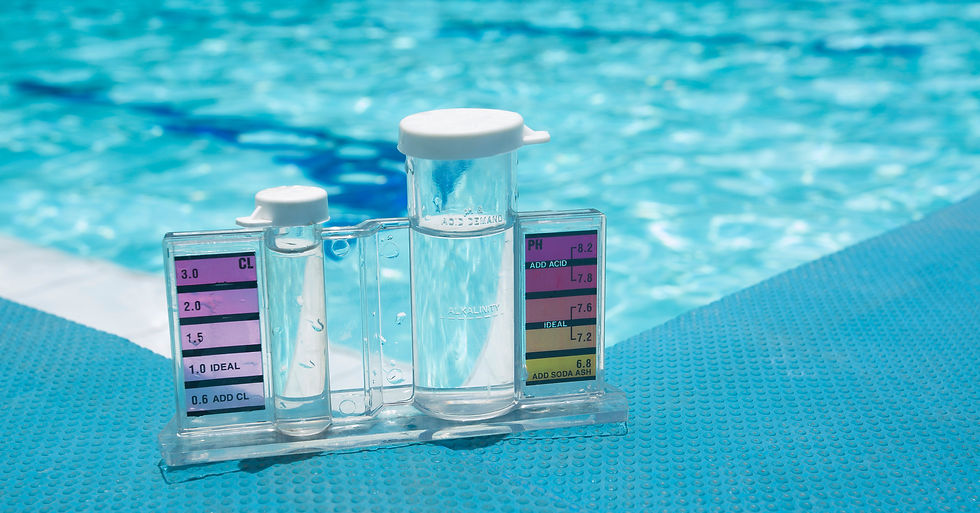
Why Quality Management Matters in ERP
Quality management is essential for manufacturing, distribution, and supply chain operations.
Poor quality control can lead to product recalls, compliance issues, and customer dissatisfaction.
Microsoft Dynamics 365 provides built-in quality management tools to:
Enforce quality checks throughout production and supply chains.
Track defects and deviations from quality standards.
Maintain regulatory compliance in highly controlled industries.
This guide explains how to set up and optimize quality management workflows in Dynamics 365.
Key Components of Quality Management in Dynamics 365
Quality Orders
A Quality Order is a structured inspection process used to verify product quality.
Can be triggered by:
Purchase order receipts – Inspecting raw materials upon delivery.
Production order completions – Checking finished goods before shipment.
Customer returns – Validating returned products before restocking.
Periodic inspections – Conducting scheduled quality checks.
Users record inspection results, pass/fail criteria, and corrective actions.
Quality Associations (Automating Quality Checks)
Define when and where quality orders are automatically created.
Triggers can be set for specific vendors, production batches, or inventory items.
Example: Automatically generate a quality order for every batch of pharmaceuticals received from a supplier.
Inventory Blocking for Quality Control
Prevents defective products from being used until an inspection is complete.
Items under inspection can be temporarily blocked until quality approval.
If an item fails inspection, it can be moved to:
Rework – Sent for repair or modification.
Scrap – Discarded if unusable.
Return to vendor – Sent back if supplier quality is insufficient.
Nonconformance Management
Tracks defective materials, failed inspections, and process deviations.
Corrective actions can be assigned to specific employees or teams.
Example: If 5% of products fail an inspection, an investigation is automatically triggered.
Corrective and Preventive Actions (CAPA)
Ensures defects are analyzed, reported, and resolved to prevent recurrence.
CAPA workflows track:
Root cause analysis – Identifying why defects occurred.
Corrective actions – Fixing the immediate issue.
Preventive actions – Improving processes to avoid future defects.
How to Set Up a Quality Management Workflow in Dynamics 365
Define Quality Associations
Navigate to Quality Management > Quality Associations.
Set up rules for when quality orders should be created.
Define inspection parameters based on supplier, product, or production batch.
Configure Quality Test Parameters
Set tests and tolerances for specific items (e.g., weight, dimensions, material composition).
Define acceptable limits for pass/fail criteria.
Example: In pharmaceuticals, a tablet's active ingredient concentration must be within 95% to 105% of the label claim.
Automate Inventory Blocking for Inspection
Go to Inventory Management > Quality Management.
Enable automatic inventory blocking for incoming stock or production orders.
Ensure quality inspection approval before goods are released for sale or manufacturing.
Assign Corrective Actions for Failed Quality Checks
When a product fails inspection, create a nonconformance record.
Assign corrective actions to responsible teams (e.g., production, supply chain, or vendor management).
Track progress and resolution timelines within Dynamics 365.
Generate Quality Reports and Audit Logs
Use Power BI or built-in Dynamics 365 reports to track quality trends.
Monitor failure rates, supplier quality performance, and corrective action effectiveness.
Audits based on recorded quality history are conducted to ensure regulatory compliance.
Best Practices for Optimizing Quality Management in Dynamics 365
Standardize Inspection Criteria
Define clear quality specifications for every product or material.
Ensure quality inspectors use consistent testing procedures across different batches.
Train Employees on Quality Management Features
Provide training for warehouse staff, production teams, and suppliers on using quality orders.
Encourage real-time data entry and automated tracking of quality control results.
Integrate IoT for Real-Time Quality Monitoring
Connect IoT sensors to Dynamics 365 for automated defect detection.
Example: A manufacturing plant can use temperature sensors in a chemical production process to trigger quality alerts if conditions go outside acceptable limits.
Establish Supplier Quality Scorecards
Track supplier performance based on quality pass/fail rates.
Automate vendor scorecards to identify high-risk suppliers.
Example: If a supplier consistently delivers defective parts, future purchase orders can be flagged for mandatory quality inspection.
Use AI and Machine Learning for Predictive Quality Analysis
Based on historical data, AI-driven analytics can predict which batches are more likely to have defects.
Predictive analytics helps identify trends in material failures before they cause production delays.
Industry Applications of Quality Management in Dynamics 365
Manufacturing
Ensures defective products do not reach customers.
Automates quality testing for raw materials, in-process goods, and finished products.
Pharmaceuticals and Healthcare
Maintains strict compliance with FDA and GMP regulations.
Tracks batch consistency, active ingredient potency, and expiration dates.
Retail and Consumer Goods
Prevents defective goods from being shipped to customers.
Ensures compliance with safety and labeling regulations.
Food and Beverage
Monitors food safety compliance (temperature, contamination risk, ingredient quality).
Reduces recalls and product contamination risks.
Why Quality Management in Dynamics 365 is Essential
Implementing quality management in Dynamics 365 ensures:
Higher product standards
Fewer defects
Better compliance
Businesses that automate quality inspections and corrective actions experience:
Fewer customer complaints
Reduced waste and lower operational costs
Leveraging AI, IoT, and Power BI reporting further enhances predictive quality monitoring and process improvements.
Comments